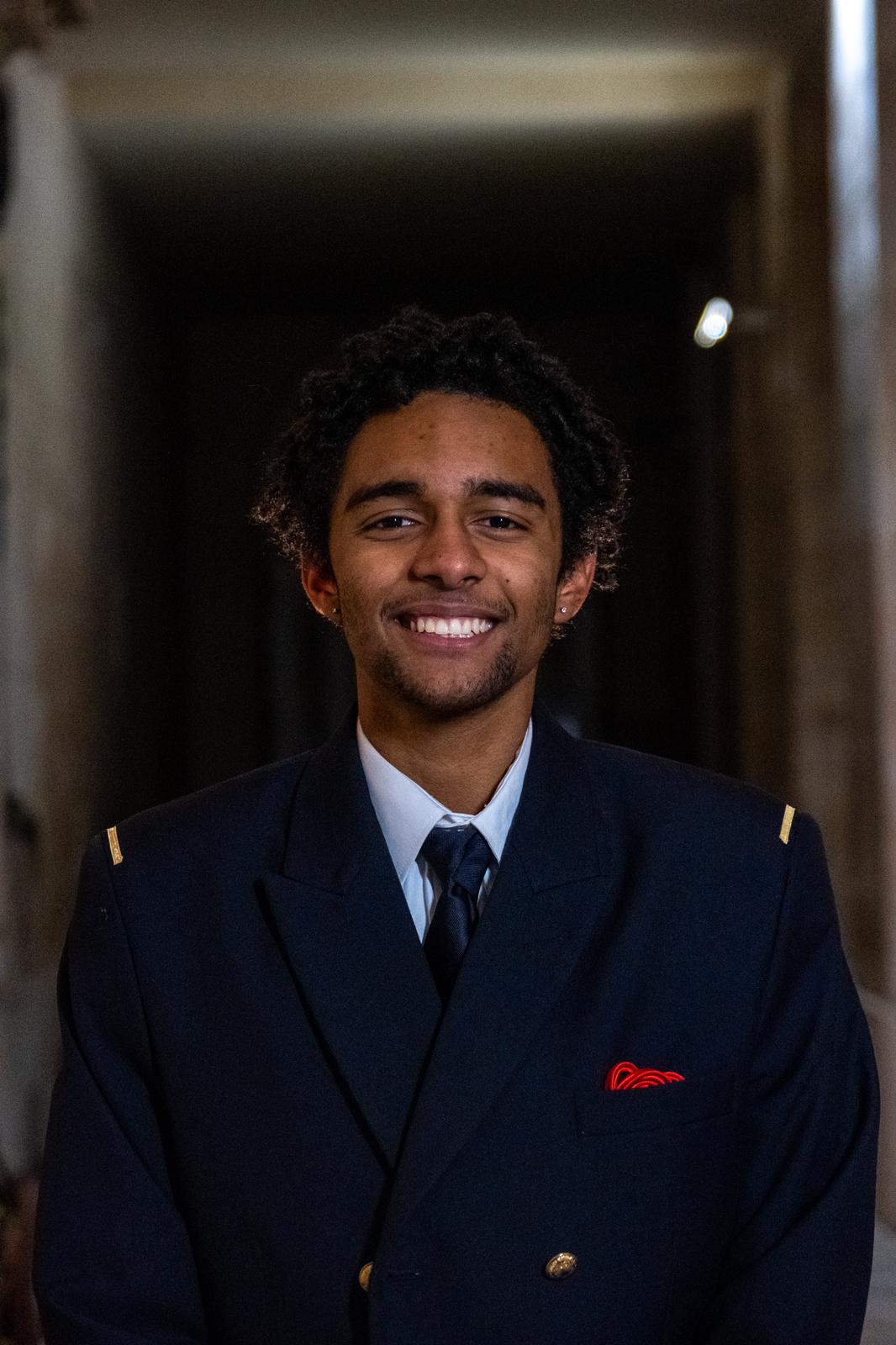
Clément Dumeril
Master of Science in Engineering Student
Arts et Métiers
About Me
I am Clément Dumeril, a mechanical engineering student at Arts et Métiers, with a passion for solving real-world problems through engineering. Whether designing a Helmholtz-based acoustic system, developing an industrial 8.5kW gearbox, or integrating AI into engineering workflows at TechWave, I always seek to turn technical challenges into practical innovations. Beyond engineering, I led business and technical projects at AMJE, building strong leadership, teamwork, and entrepreneurial skills. Growing up between France and Tanzania has shaped a global mindset, pushing me to think beyond borders and design solutions that matter. At Berkeley, I am excited to deepen my expertise in mechanics, energy systems, and innovation, while contributing to a community that values collaboration, bold ideas, and impact. I am ready to work hard, think big, and engineer solutions that help build a better, more sustainable world.
Interests
- Artificial Intelligence Applications in Engineering
- Smart Manufacturing and Industry 4.0
- Global Engineering Challenges
- Sustainable Design
Education
Timeline
European German Baccalaureate, Honors
Lycée Michelet, Vanves, France. Specialization in Engineering Sciences.
Preparatory Classes for Engineering Schools (PTSI/PT*)
Lycée Raspail, Paris, France. Intensive preparation for national engineering competitive exams.
Arts et Métiers
Master's Degree in Mechanical Engineering. Technical projects, leadership roles, international exposure.
Major Projects
Low-tech Refrigerator, Industrial Gear Reducer, Acoustic Research, AI Integration in Engineering.
Professional Experiences
R&D Internship, Business Manager at AMJE, consulting projects, team management experience.
Major projects
Low-Tech Refrigerator Design Project
Sustainable engineering project conducted at Arts et Métiers (ENSAM), focused on the design and thermal dimensioning of a low-energy refrigerator system using air as a refrigerant.
As part of a mechanical design studio in the first year of engineering studies, our team of five students tackled the challenge of designing an environmentally friendly, locally manufacturable refrigerator aimed at minimizing energy consumption and maximizing accessibility in rural or low-resource areas.
The project covered the entire development cycle:
- Functional analysis and stakeholder mapping (SWOT, user scenarios, environmental context)
- Benchmarking of existing low-tech and commercial refrigeration solutions
- Architectural and structural design with material selection, ergonomics, and mechanical integration
- Thermal modeling of the system based on a reversed Joule cycle using air as a refrigerant
- Compressor and heat exchange surface sizing based on realistic energy loads and insulation losses
- Lifecycle analysis and eco-design strategies for sourcing, manufacturing, and end-of-life recyclability
The system was dimensioned to hold 100 L, maintain 5°C internal temperature, and operate with a peak cooling power of ~7W in a closed air circuit, powered by a low-wattage compressor. Tubing diameter, air velocity, losses, and cycle performance were evaluated using engineering formulas and expert input.
This project helped us develop rigorous design methodology, apply thermal and mechanical calculation methods, and integrate user-centered low-tech thinking into the design of a modern sustainable product.
Preview Full Report (PDF)Mechanical Gear Reducer Design
Engineering project on dimensioning, modeling, and validating a 4:1 industrial gear reducer designed to transmit 8.5 kW of power continuously over 22,000 hours.
This project was carried out at Arts et Métiers (ENSAM) as part of our Mechanical Design Studio coursework. It followed the full methodology of a pre-production design, under the supervision of Professor Jean-Marc Périnet. Our team was responsible for producing a functional, cost-effective, and manufacturable gearbox intended for small-batch industrial use.
We began with an in-depth analysis of the functional specifications, followed by benchmarking of existing solutions. We identified key constraints related to mechanical efficiency, space, lifetime, and thermal management. Our technical process included:
- Definition of functions and technical constraints based on usage scenarios and lifecycle
- Selection of gear type via weighted decision matrices (gear vs. chain vs. belt)
- Calculation and optimization of gear geometry: module, tooth number, width (using Excel + Engrenage.exe)
- Pre-dimensioning of shafts using Tresca stress criteria and elasticity constraints
- Mechanical modeling of internal forces on gears and bearings under operating load
- CAD architecture including mounting strategy, lubrication channels, housing shape, and ease of maintenance
- Component selection (bearings from SKF, seals from Paulstra, standardized bolts)
- Clavette and coupling analysis to ensure torque transmission without failure
The final solution features a spur gear pair (12/48 teeth, module 5 mm), with a steel housing, standardized mounting plate, and integrated maintenance points. All parts were cross-checked for manufacturing compatibility and supplier availability.
This project gave me a solid grounding in real-world mechanical system design: from modeling and simulation, to tolerancing, cost analysis, and physical integration.
Preview Full Report (PDF)Manufacturing of a Pump Body
Manufacturing engineering project carried out at Arts et Métiers (ENSAM), focused on the complete realization of a pump body from casting to machining and dimensional control.
This project was part of a full-cycle manufacturing training. The goal was to understand the complete industrial process involved in producing a functional pump body, covering three major stages: foundry, machining (manual and CNC), and metrology. The part had to meet precise dimensional specifications and be machinable under real conditions.
Phase 1: Foundry
We designed the casting mold in sand, taking into account draft angles, joint plane, vents, shrinkage, and machining allowances (~3 mm). The chosen alloy was AlSi7, and molding was done by manually compacting clay-bound sand. Our process ensured proper porosity and minimized alumina skin defects. The final casting showed realistic imperfections (surface granularity, mismatch at the joint plane) which were analyzed and documented.
Phase 2: Machining
Machining was split into two sub-phases:
- Phase 100: Manual turning – Facing and boring using fixed-tool lathe. Low-speed cuts due to machine limitations. High tool wear observed due to sand residues from casting.
- Phase 200: CNC turning – Tool path calibration via probing. CAD model used to define operations on faces C, D, E (facing, grooving, internal boring). Higher precision and surface finish, suitable for series production.
Phase 3: Metrology
Dimensional control was conducted using a robotic coordinate measuring machine equipped with a 3-point electric contact probe. We checked flatness, perpendicularity, and cylindricity (plan E, surfaces C/D/E). Gauss fitting and tolerance analysis confirmed proper positioning but revealed non-compliance for tight cylindricity due to raw casting limitations.
This hands-on project helped us experience real-world manufacturing challenges: material choice, tool selection, machine wear, tolerance validation, and quality control. It reinforced our understanding of manufacturing interdependencies and the cost-performance tradeoffs in industrial part production.
Preview Full Report (PDF)Acoustic Filtering Using Helmholtz Resonators
Scientific research project on passive control of low-frequency sound using acoustic resonance systems.
This project was carried out in 2024 as part of the French Classe Préparatoire aux Grandes Écoles (equivalent to elite undergraduate engineering preparation), and evaluated by professors from top national programs. It earned a final score of A following a formal jury presentation.
The objective was to study how Helmholtz resonators can be used to attenuate low-frequency “droning” noise (150–300 Hz) in acoustic systems. I designed a tunable, passive solution applicable to ducts or exhaust systems by combining theoretical modeling, experimental validation, and numerical simulation.
The work followed a rigorous scientific process:
- Analytical derivation of the resonance frequency, impedance model, and quality factor (Q), starting from acoustic mass-spring systems
- Prototype fabrication using PVC resonators and pressure measurement via calibrated microphone and REW software
- Quantitative analysis of acoustic gain and transmission loss (TL), including comparison between measured, simulated (COMSOL), and theoretical data
- System extension with coupled resonators (DSRH) to broaden the attenuation bandwidth and mitigate anti-resonance effects
The project demonstrated over 30 dB attenuation in targeted frequency bands and validated the precision of Helmholtz-based modeling in real conditions. It strengthened my scientific skills in applied acoustics, mathematical modeling, data acquisition, and experimental uncertainty analysis.
Preview Full Report (PDF)